A Glimpse Inside the Porsche Paint Shop
Robots and AI streamline Porsche's paint inspection process, ensuring precision, speed, and high-quality standards with automated defect detection.
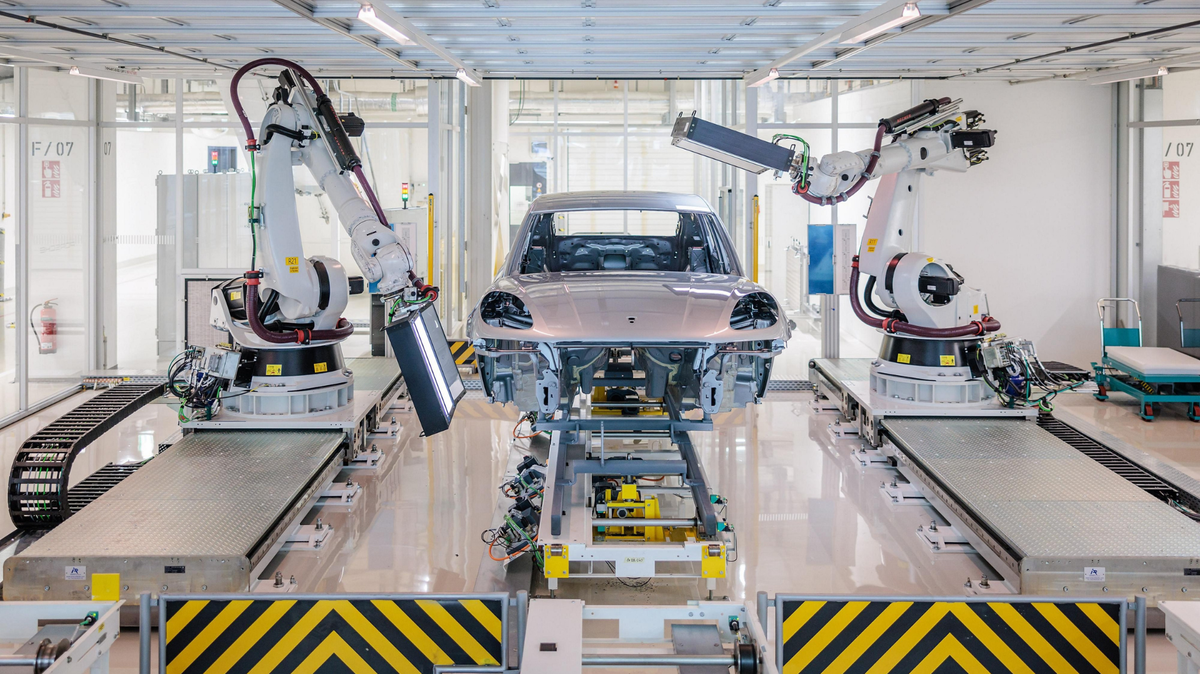
For decades, robots have been used to apply paint to new cars during manufacture, improving safety for employees while yielding the benefits of increased efficiency and more consistent paint application. But even with the precision and reproducibility of robot-applied finishes, vehicles still need to be visually checked to identify any potential paint defects.
Until recently, these labour-intensive and time-consuming inspections had to be performed manually, and even with the sharpest eyes, there was always the natural risk of human error. However, thanks to modern technology, the process in the paint shop at Porsche’s Leipzig plant has been significantly streamlined. Here, inspection team members are supported by an automatic defect detection system featuring two robots, designed specifically for this task. Although these robots are similar to those used on the painting line, they are configured differently for inspection purposes. Equipped with advanced sensors, the robotic arms scan the entire outer surface of every body shell produced at Leipzig. An image is taken every 2.5 millimetres, resulting in approximately 100,000 images captured during the 72-second inspection cycle. These extensive scans are then analysed by a network of 10 powerful image-processing computers that search for even the smallest imperfections. Pinholes, craters, and dust particles (referred to as ‘inclusions’) are identified with precision and objectivity, which offers a significant advantage over the subjective nature of manual inspections.

If a defect is detected, its exact location is recorded with millimetre accuracy. The complete data is forwarded to the finishing line, where the skilled team addresses the necessary paint corrections. The exact location of the defect is displayed on a detailed 3D model, which includes high-resolution close-up images and information on the defect type, enabling the team to quickly pinpoint the issue and select the appropriate corrective method.
Each issue is automatically recorded, categorised, and analysed through AI and deep learning algorithms. This enables the identification of any emerging trends in defect types or locations, ensuring that any unwanted process variations are spotted early and facilitating ongoing optimisation of the painting process.
The use of this technology greatly boosts efficiency while maintaining Porsche's high-quality standards. What was once a slow and labour-intensive inspection process is now fully automated, with the entire scanning and evaluation process completed in under 100 seconds.